Choosing the Right Copper: The Industrial Shift to Oxygen-Free Copper Explained
In industries where performance, durability, and conductivity are critical, oxygen-free copper (OFC) is becoming the material of choice. Its superior properties compared to traditional pure copper make it invaluable in applications ranging from electronics to aerospace. This guide explores the benefits of OFC, its manufacturing process, and how it compares to pure copper, helping you make an informed decision for your industrial needs.
Oxygen-free copper is a high-purity copper alloy with minimal oxygen content, typically less than 0.001%. It is produced using a refining process that removes oxygen and other impurities, resulting in enhanced electrical and thermal conductivity, superior durability, and excellent resistance to oxidation.
Key Characteristics of Oxygen-Free Copper
- High Conductivity: Enhanced electrical and thermal conductivity due to reduced impurities.
- Corrosion Resistance: Superior resistance to oxidation and corrosion.
- Mechanical Strength: Improved ductility and strength, making it suitable for high-stress applications.
- Purity: Contains at least 99.95% copper, ensuring consistent performance.
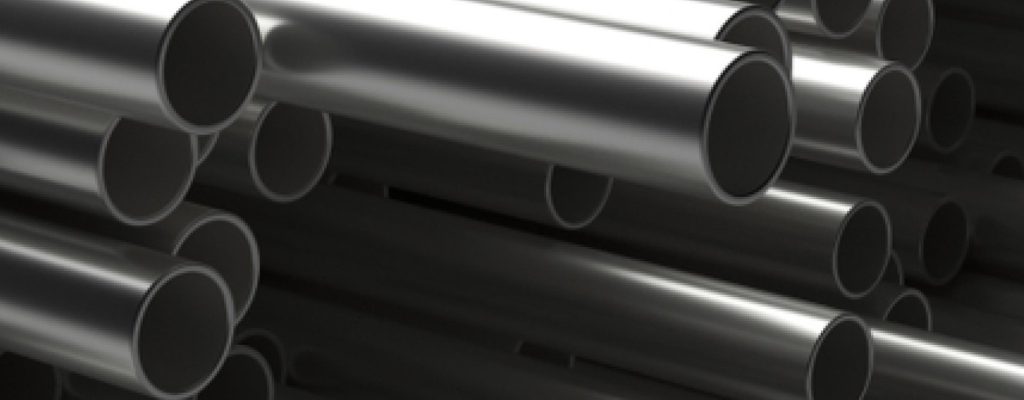
Oxygen-Free Copper vs. Pure Copper
Property | Oxygen-Free Copper | Pure Copper |
---|---|---|
Purity | 99.95% or higher | 99.90% or lower |
Conductivity | Higher electrical and thermal conductivity | Lower conductivity due to impurities |
Oxidation Resistance | Excellent | Moderate |
Mechanical Properties | Enhanced strength and ductility | Lower strength and ductility |
Cost | Higher | Lower |
Why Choose OFC Over Pure Copper?
- OFC is ideal for applications where high conductivity and resistance to oxidation are critical, such as in aerospace, electronics, and power generation.
- Pure copper is more cost-effective but may lack the performance advantages required in demanding environments.
Applications of Oxygen-Free Copper
- Electronics and Audio Systems
- Oxygen-Free Copper Wires: Used in high-end audio and video systems for superior signal clarity.
- Why OFC? High conductivity minimizes signal loss and distortion.
- Heat Exchangers
- Oxygen-Free Copper Tubes and Pipes: Essential in HVAC systems, refrigeration, and heat exchangers.
- Why OFC? Excellent thermal conductivity ensures efficient heat transfer.
- Aerospace and Defense
- Oxygen-Free Copper Sheets: Used in aerospace components requiring high thermal resistance and structural integrity.
- Why OFC? High purity reduces the risks of material failure in extreme conditions.
- Medical Equipment
- Oxygen-Free Copper Components: Found in medical imaging systems and surgical devices.
- Why OFC? Biocompatibility and reliability are critical in sensitive applications.
- Renewable Energy
- Oxygen-Free Copper Conductors: Used in solar panels and wind turbines for efficient energy transfer.
- Why OFC? High conductivity improves overall system efficiency.
Key Oxygen-Free Copper Products
- Oxygen-Free Copper Pipes
- Applications: Plumbing, HVAC, and refrigeration systems.
- Benefits: Corrosion resistance ensures long service life.
- Oxygen-Free Copper Tubes
- Applications: Heat exchangers, solar collectors, and automotive cooling systems.
- Benefits: Superior thermal conductivity enhances efficiency.
- Oxygen-Free Copper Sheets
- Applications: Aerospace, defense, and electronic shielding.
- Benefits: High ductility allows for precise machining and shaping.
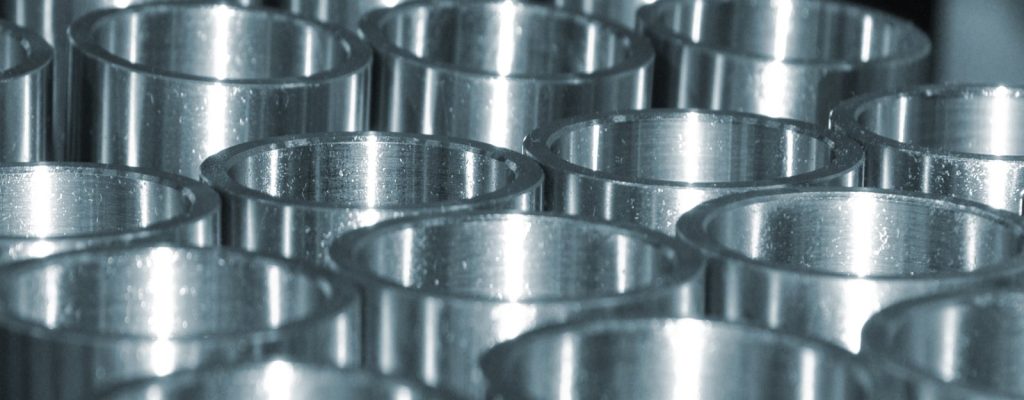
How Oxygen-Free Copper is Manufactured
- Refining Process: OFC is produced through electrolytic refining or vacuum melting, which removes oxygen and impurities.
- Casting: The refined copper is cast into billets, rods, or slabs, ensuring high purity and uniformity.
- Forming: Copper is rolled, drawn, or extruded into pipes, tubes, sheets, or wires depending on the application.
- Quality Assurance: Rigorous testing ensures compliance with international standards such as ASTM B170 for oxygen-free copper.
Future Trends in Oxygen-Free Copper
- Increased Demand in Renewable Energy: The growing adoption of solar panels, wind turbines, and electric vehicles is driving demand for high-conductivity OFC.
- Advancements in Electronics: As devices become smaller and more powerful, the need for reliable, high-performance materials like OFC is rising.
- Sustainability Focus: Manufacturers are emphasizing recycled OFC to meet environmental regulations and reduce waste.
- Expansion in Aerospace Applications: Lightweight, high-strength OFC components are becoming integral to modern aerospace designs.
Conclusion
Oxygen-free copper is the material of choice for industries requiring superior conductivity, corrosion resistance, and mechanical performance. From oxygen-free copper pipes to oxygen-free copper sheets, its versatility and reliability make it indispensable in modern engineering and technology.
Looking for high-quality oxygen-free copper products? Partner with a trusted manufacturer to access premium materials tailored to your industry needs. Contact us today for expert advice and customized solutions.

Need Help?
We're Here for You!
Feel free to contact us any time. we will get back to you as soon as we can!
Ask Anything
OFC has higher purity and conductivity, offering superior performance in applications requiring minimal oxidation and maximum efficiency.
OFC is widely used in electronics, aerospace, medical equipment, renewable energy, and HVAC systems.
Yes, due to its refining process and higher purity, OFC costs more than pure copper but offers significant performance benefits.